Jacob Ward Portfolio
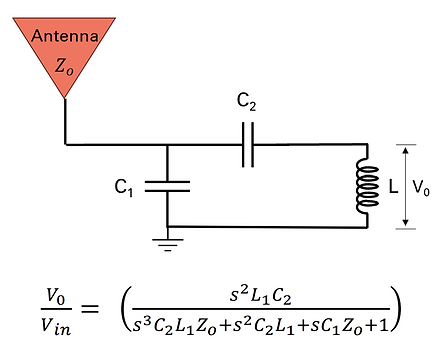
Overview
This project explores the design and optimization of a variable MEMS capacitor for real-time antenna tuning in RF circuits. Utilizing a comb-drive actuator design for C2 in the Pi-filter, the device dynamically adjusts capacitance to compensate for variations in antenna impedance Z0 around its nominal value of 50 Ω. See the final IEEE report and presentation for more detailed information about the project.
Methodology
Consisting of fixed capacitor C1, inductor L, and variable MEMS capacitor C2, the filter is designed with a center frequency of 2.4 GHz to support common wireless communication bands. The comb drive variable MEMS capacitor was designed to enable precise capacitance tuning through electrostatic actuation. Precise voltages applied across the fingers induce electrostatic forces that push/pull the movable fingers, altering the capacitance with the change in overlapping area. Key parameters such as finger thickness, length, and the number of movable fingers were optimized to achieve maximum tuning range while minimizing power consumption and footprint.
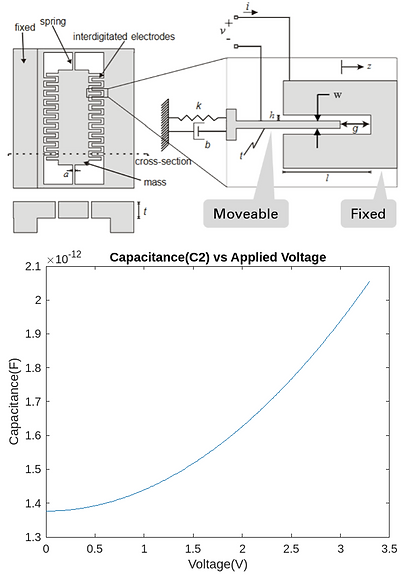

Implementation
The mechanical behavior of the comb drive was modeled to ensure a balance between electrostatic force and the restoring force provided by the integrated spring structure. A series of optimization analyses were conducted to determine the ideal design parameters for the comb drive. A MATLAB sweep analysis was performed (with constant C1 = 1.206 pF and C2 = 1.666 pF) that revealed an ideal inductor value of L = 2.64 nH to minimize the number of capacitance fingers in the comb drive and the number of fingers in the spring structure at 187. The study identified a balance between performance and physical constraints, allowing the capacitor to achieve a tunable range of 2.056 pF to 1.367 pF for input voltages between 0 V and 3.3 V, respectively.
Microfabrication Processes
Two distinct microfabrication processes were proposed for manufacturing the MEMS capacitor. The first process, shown below, used LPCVD, DRIE etching, and lift-off techniques to fabricate the silicon-based comb drive structure. This method ensured precise feature definition but required careful control over deposition and etching steps. The second process leveraged electroplating and low-temperature fabrication to minimize residual stress in the comb structure, improving structural integrity and manufacturability. Both methods were evaluated based on feasibility, cost-effectiveness, and compatibility with modern MEMS fabrication techniques and are outlined in further detail in the report.
